An engineered high temperature resistant steel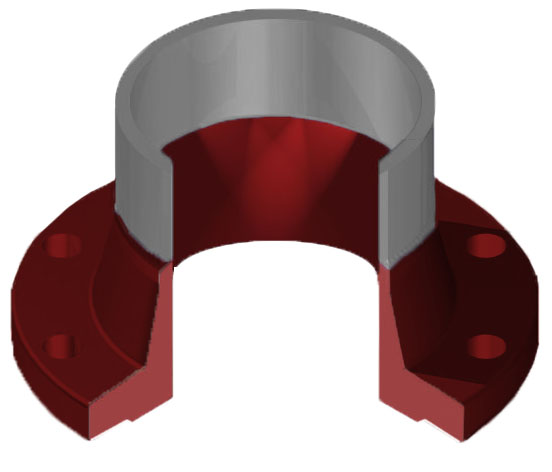
- Excellent high temperature stability strength
- Very oxidation and carburization resistant to 2100°F
- Good resistance to thermal shock and quenching
- Chemistry and specifications of Alloy 330
- Weld neck flange features and benefits
- Alloy 330 Datasheet
Alloy 330 weld neck flanges are specifically designed for high temperature furnace applications such as vacuum furnaces, heat treating and brazing applications. The most prized trait of alloy 330 is its ability perform under cyclic conditions of temperature extremes from heating and cooling; as well as in alternate carburizing and oxidizing atmospheres. An austenitic nickel-chromium-iron-silicon alloy, 330 weld neck flanges also offer industry a low coefficient of expansion, excellent ductility, and high strength.
Benefits & Corrosion Resistance
- Resistance to thermal shock from repeated quenching
- High level of resistance to oxidation and carburization
- Ability to handle thermal cycling
- Provides resistance to scale formation up to about 2000°F
- Good resistance to nitrogen-containing atmospheres where the oxygen content is low
- High nickel content of 34-37% provides high resistance to chloride stress corrosion cracking and embrittlement
Applications for Alloy 330 Weld Neck Flanges
- Alloy 330 flanges are often used in furnaces, thermal processing and heat treating applications.
- Gas turbine components and boiler fixtures used in power generation often use Alloy 330 weld neck flanges.
- Because of its resistance to nitrogen rich environments, alloy 330 flanges are used extensively for components handling cracked ammonia.
Alloy 330 Properties | |
Tensile Strength (ksi) | 80-85 |
Yield Strength (ksi) | 30-43 |
Elongation in 2” | 40-45 |
Rockwell B Hardness | 70-85 |
Density (lb/in3) | 0.292 |
Specific Heat (Btu/lb/°F (32°-212°F) | 0.11 |
Modulus of Elasticity Tension | 28.5 |
Resources: Alloy 330 Torque Specs, Flange Dimensions, Flange Bolting Chart
Flange Types Available: Blind Flanges, Lap Joint Flanges, Slip On Flanges, Socket Weld Flanges, Threaded Flanges, Weld Neck Flanges
Alloy 330 Weld Neck Flange Features & Benefits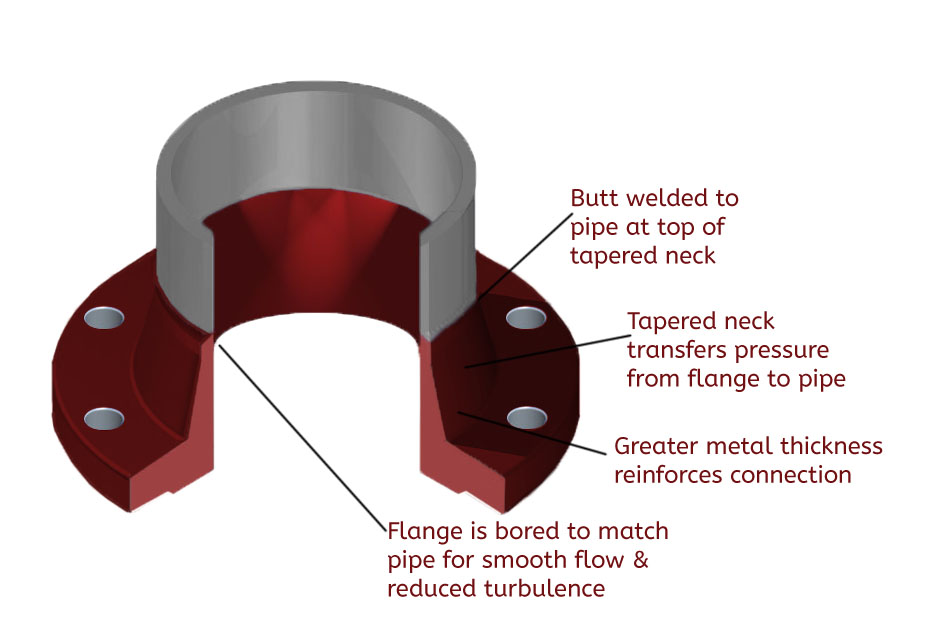
Alloy 330 weld neck flanges are best for hazardous, high pressure applications. Weld neck flanges are easily identified by their long tapered neck. The inside of the flange is bored to match the inside diameter of the pipe in order to ensure there is no restriction in flow and also to prevent turbulence at the joint. The tapered neck provides thicker metal at the flange joint, while the neck narrows down gradually to meet the pipe where it is butt welded to the pipe. This design helps to transfer stress from the flange to the pipe, as well as diminish stress concentration at the base of the flange connection.
Alloy 330 weld neck flanges are ideal for critical applications involving high pressure, sub-zero and elevated temperatures, as well as in conditions where fluctuations cause pipe expansion/contraction.
Key Feature: Ideal for high presure applications.
Weld Neck Flange Advantages
- Ability to withstand high pressure – since pipe is welded to the neck of the flange, stress is transferred to the pipe.
- The beveled end that, when connected to a pipe, creates a trough for a strong weld.
- Most versatile flange in the ASME stable of flanges.
Weld Neck Flange Disadvantages
- More advanced welding skill is needed for installation. The inside weld must be smooth to reduce friction and the outside weld must meet code criteria.
Uses
- Severe conditions that include high-pressure, high-cyclic and hazardous fluid applications.
- Fitting-to-fitting fabrication where the flange is welded directly to a fitting, such as an elbow, without the need for a short piece of pipe, as would be required with a slip-on flange.
Alloy 330 Chemistry and Specifications
Alloy 330 (UNS N08330) is best known for its extreme high temperature strength and stability. One of the most unique attributes of Alloy 330 is its ability to handle cyclic temperature changes from extreme high temperatures to cooling phases, as well as in oxidation-rich environements.
Alloy 330 Specifications: UNS N08330, AMS 5592, AMS 5716, ASME SB 511, ASME SB 536, ASTM B 511, ASTM B 512, ASTM B 535, ASTM B 536, ASTM B 546, ASTM B 710, ASTM B 739, EN 10095, Werkstoff 1.4886