An engineered high temperature resistant steel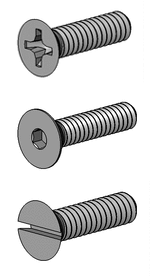
- Excellent high temperature stability and strength
- Very oxidation and carburization resistant to 2100°F
- Good resistance to thermal shock and quenching
- Chemistry and specifications of alloy 330
- Alloy 330 flat head screw features and benefits
- Datasheet for Alloy 330
Alloy 330 flat head screws are specifically designed for high temperature furnace applications such as vacuum furnaces, heat treating and brazing applications. The most prized trait of alloy 330 is its ability perform under cyclic conditions of temperature extremes from heating and cooling; as well as in alternate carburizing and oxidizing atmospheres. An austenitic nickel-chromium-iron-silicon alloy, 330 flat head screws also offer industry a low coefficient of expansion, excellent ductility, and high strength.
Benefits & Corrosion Resistance
- Resistance to thermal shock from repeated quenching
- High level of resistance to oxidation and carburization
- Ability to handle thermal cycling
- Provides resistance to scale formation up to about 2000°F
- Good resistance to nitrogen-containing atmospheres where the oxygen content is low
- High nickel content of 34-37% provides high resistance to chloride stress corrosion cracking and embrittlement
Applications for Alloy 330 Flat Head Screws
- Alloy 330 screws are often used in furnaces, thermal processing and heat treating applications.
- Gas turbine components and boiler fixtures used in power generation often use Alloy 330 flat head screws.
- Because of its resistance to nitrogen rich environments, alloy 330 screws are used extensively for components handling cracked ammonia.
Alloy 330 Properties | |
Tensile Strength (ksi) | 80-85 |
Yield Strength (ksi) | 30-43 |
Elongation in 2” | 40-45 |
Rockwell B Hardness | 70-85 |
Density (lb/in3) | 0.292 |
Specific Heat (Btu/lb/°F (32°-212°F) | 0.11 |
Modulus of Elasticity Tension | 28.5 |
Resources: Alloy 330 Torque Specs
Alloy 330 Screw Types: 12 Point Screws, Button Head Cap Screws, Flat Head Screws, Hex Head Cap Screws, Pan Head Screws, Set Screws, Socket Head Cap Screws, Tamper Resistant Security Screws, Torx Screws, Vented Screws
Alloy 330 Flat Head Screw Features and Benefits
Alloy 330 flat head screws are characterized by having a head with a top flat surface (which can feature either a slotted, phillips or allen driver) and bottom that is cone shaped or countersunk. With this design, the head of the screw can align flush or below the surrounding surface having obvious benefits.
Alloy 330 Slotted vs. Phillips Driver
Slotted Head Advantages | Phillips Head Advantages |
|
|
Countersink Angle
For most flat head screw designs the angle of countersink is usually 82° for UNC and UNF applications however other angles ranging from 60° -120° could be specified.
Thread Type | Normal Flat Head Countersink Angle |
UNC / UNF | 82° |
Aerospace | 100° |
ISO Metric / Imperial | 90° |
Alloy 330 Chemistry and Specifications
Alloy 330 (UNS N08330) is best known for its extreme high temperature strength and stability. One of the most unique attributes of Alloy 330 is its ability to handle cyclic temperature changes from extreme high temperatures to cooling phases, as well as in oxidation-rich environements.
Alloy 330 Specifications: UNS N08330, AMS 5592, AMS 5716, ASME SB 511, ASME SB 536, ASTM B 511, ASTM B 512, ASTM B 535, ASTM B 536, ASTM B 546, ASTM B 710, ASTM B 739, EN 10095, Werkstoff 1.4886