Good high temperature oxidation resistance to 2000°F
High temperature stability for moderate strength applications- Good oxidation and carburization resistant to 2000°F
- Resistance to moderate sulfidation and nitriding
- Economic alternative to high temperature nickel alloys
- 310SS chemistry & specifications
- Features & benefits of 310SS lap joint flanges
- Datasheet for 310 stainless steel
Designed for high temperature applications, 310 stainless steel lap joint flanges provide high temperature oxidation resistance to 2000°F under mild cyclic conditions. An economic alternative to nickel alloys like alloy 330 or Inconel, 310 flanges provide slightly less strength and temperature resistance – but at a significantly lower price point. Alloy 310 can be used in moderately caburizing, moderately oxidizing, nitriding, cementing and thermal cycling applications when not used at the maximum service temperature. 310SS lap joint flanges also have good resistance to sulfidation and other forms of hot corrosion. Although primarily known for its high temperature properties, 310 stainless steel also provides excellent performance at cryogenic temperatures, with toughness down to -450˚F. Though 310 lap joint flanges are ideal for high temperature use, they should not be exposed to the severe thermal shock of repeated liquid quenching or where aqueous corrosive contaminants are present.
Benefits
- High temperature resistance.
- Excellent resistance to oxidation under mildly cyclic conditions.
- Good resistance to sulfidation and atmospheres where sulfur dioxide gas is encountered at elevated temperatures.
- Good resistance to thermal fatigue.
- Excellent toughness to cryogenic temperatures of -450°F.
- Low magnetic permeability.
- Good ductility and weldability.
Applications
- Thermal processing and high temperature furnaces rely on 310 lap joint flanges for their high temperature and oxidation resistance in minor cyclic conditions.
- 310SS flanges are commonly used in the petrochemical industry for their ability to provide resistance to moderately carburizing atmospheres.
- The high temperature properties of 310 flanges make them ideal for ore processing, steel plants, power generation, and sintering.
- Cryogenic structures often use 310 stainless steel lap joint flanges for their strength at -450°F and low magnetic permeability.
310 Stainless Steel Properties | |
Tensile Strength (ksi) | 70 |
Yield Strength (ksi) | 30 |
Rockwell B Hardness | 95 |
Density (lb/in3) | 0.285 |
Electrical Resistivity (Microhm-in at 68°C) | 30.7 |
Modulus of Elasticity (x 106 psi) | 28.5 |
Thermal Conductivity at 212°F (BTU/hr/ft2/ft/°F) | 8.0 |
Resources: Flange Dimensions, Flange Bolting Chart
Alloy 310 Bolt Types: Blind Flanges, Lap Joint Flanges, Slip On Flanges, Socket Weld Flanges, Threaded Flanges, Weld Neck Flanges
310 Stainless Steel Chemistry & Specifications
310SS Specifications: AMS 5521, AMS 5651, ASME SA 240, ASME SA 312, ASME SA 479, ASTM A 240, ASTM A 276, ASTM A 276 Condition A, ASTM A 276 Condition S, ASTM A 312, ASTM A 479, EN 10095, UNS S31008, UNS S31009, Werkstoff 1.4845
310SS Lap Joint Flange Features & Benefits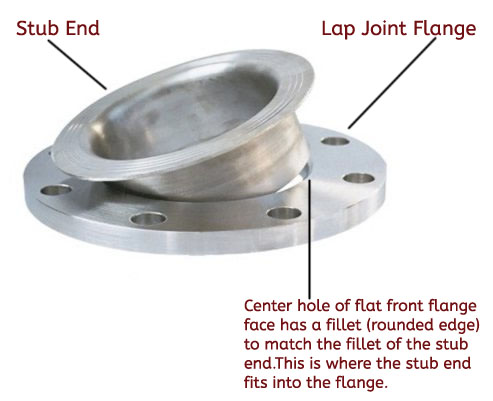
310 lap joint flanges are unique in that they are made of two pieces, the flange itself and the stub end.
Flange
- The backside, has a slight shoulder that is square cut at the center or pipe hole
- The front side has a flat face with a filleted (rounded) center hole to match the filleted back face of the stub end. Here the stub end will wrap tightly around the center hole of the flange.
Stub End
- Shaped like a short piece of pipe with a weld bevel on one. This portion of the stub end is also called the sleeve.
- Narrow shoulder on the flange facing end called is the hub. The back face of the hub has a rounded transition (or inside fillet) that joins the hub to the sleeve
Benefits
- Economy
Because a 310 lap joint flange has a two piece configuration, it offers a way to cut cost when piping systems requires - For high cost alloys the only "wetted" part is the stub end. In this situation, it is only required for the stub-end to be made of the higher cost corrosion-resistant material, where the flange itself can be the produced from lower cost steel.
- Ease of Work
By using 310SS lap joint flanges, work can be simplified in situations that require frequent and rapid disassemble and assembly during the operation of a plant. The ability to spin that backing flange compensates for misalignment of the bolt holes during assembly.