An engineered high temperature resistant steel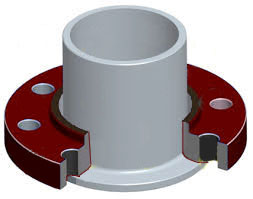
- Excellent high temperature stability and strength
- Very oxidation and carburization resistant to 2100°F
- Good resistance to thermal shock and quenching
- Chemistry and specifications for Alloy 330
- Lap joint flange features and benefits
- Alloy 330 Datasheet
Alloy 330 lap joint flanges are specifically designed for high temperature furnace applications such as vacuum furnaces, heat treating and brazing applications. The most prized trait of alloy 330 is its ability perform under cyclic conditions of temperature extremes from heating and cooling; as well as in alternate carburizing and oxidizing atmospheres. An austenitic nickel-chromium-iron-silicon alloy, 330 lap joint flanges also offer industry a low coefficient of expansion, excellent ductility, and high strength.
Benefits & Corrosion Resistance
- Resistance to thermal shock from repeated quenching
- High level of resistance to oxidation and carburization
- Ability to handle thermal cycling
- Provides resistance to scale formation up to about 2000°F
- Good resistance to nitrogen-containing atmospheres where the oxygen content is low
- High nickel content of 34-37% provides high resistance to chloride stress corrosion cracking and embrittlement
Applications for Alloy 330 Lap Joint Flanges
- Alloy 330 flanges are often used in furnaces, thermal processing and heat treating applications.
- Gas turbine components and boiler fixtures used in power generation often use Alloy 330 lap joint flanges.
- Because of its resistance to nitrogen rich environments, alloy 330 flanges are used extensively for components handling cracked ammonia.
Alloy 330 Properties | |
Tensile Strength (ksi) | 80-85 |
Yield Strength (ksi) | 30-43 |
Elongation in 2” | 40-45 |
Rockwell B Hardness | 70-85 |
Density (lb/in3) | 0.292 |
Specific Heat (Btu/lb/°F (32°-212°F) | 0.11 |
Modulus of Elasticity Tension | 28.5 |
Resources: Alloy 330 Torque Specs, Flange Dimensions, Flange Bolting Chart
Flange Types Available: Blind Flanges, Lap Joint Flanges, Slip On Flanges, Socket Weld Flanges, Threaded Flanges, Weld Neck Flanges
Alloy 330 Lap Joint Flange Features & Benefits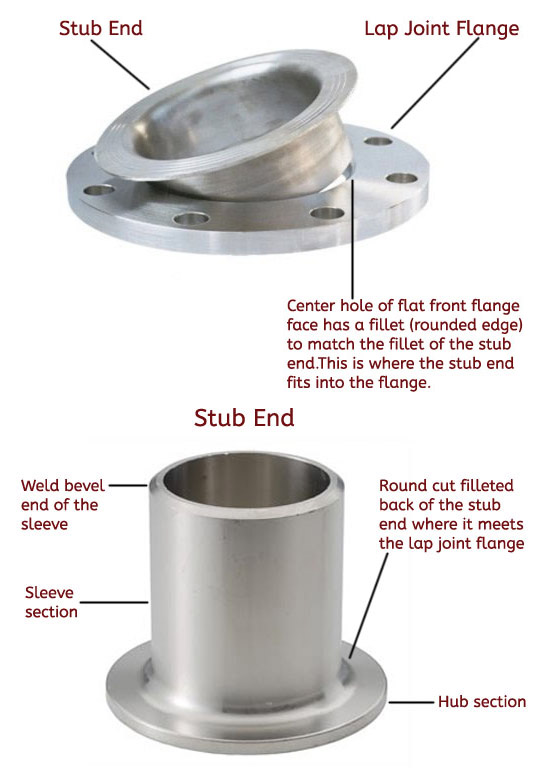
Lap joint flanges are unique in that they are made of two pieces, the flange itself and the stub end.
Flange
- The backside, has a slight shoulder that is square cut at the center or pipe hole
- The front side has a flat face with a filleted (rounded) center hole to match the filleted back face of the stub end. Here the stub end will wrap tightly around the center hole of the flange.
Stub End
- Shaped like a short piece of pipe with a weld bevel on one. This portion of the stub end is also called the sleeve.
- Narrow shoulder on the flange facing end called is the hub. The back face of the hub has a rounded transition (or inside fillet) that joins the hub to the sleeve
Benefits
- Economy
Because a lap joint flange has a two piece configuration, it offers a way to cut cost when piping systems requires - For high cost alloys the only "wetted" part is the stub end. In this situation, it is only required for the stub-end to be made of the higher cost corrosion-resistant material, where the flange itself can be the produced from lower cost steel.
- Ease of Work
By using lap joint flanges, work can be simplified in situations that require frequent and rapid disassemble and assembly during the operation of a plant. The ability to spin that backing flange compensates for misalignment of the bolt holes during assembly.
Alloy 330 Chemistry and Specifications
Alloy 330 (UNS N08330) is best known for its extreme high temperature strength and stability. One of the most unique attributes of Alloy 330 is its ability to handle cyclic temperature changes from extreme high temperatures to cooling phases, as well as in oxidation-rich environements.
Alloy 330 Specifications: UNS N08330, AMS 5592, AMS 5716, ASME SB 511, ASME SB 536, ASTM B 511, ASTM B 512, ASTM B 535, ASTM B 536, ASTM B 546, ASTM B 710, ASTM B 739, EN 10095, Werkstoff 1.4886