A high performace nickel alloy used for severe corrosion environments
- Excellent corrosion resistance to reducing and oxidizing environments
- Well suited for hydrochloric and sulfuric acid environments
- Strong resistance to stress corrosion cracking
- Excellent mechanical properties at elevated temperatures
- Alloy grades: C276, B2, B3, C22, Hastelloy X
- Weld neck flange features and benefits
Hastelloy® fasteners & flanges are in stock and available now - such as Hastelloy C276, which is generally considered a versatile and highly corrosion resistant alloy. Hastelloy weld neck flanges have excellent corrosion resistance in both oxidizing and reducing media which makes it well suited for a variety of strong corrosive applications. Hastelloy weld neck flanges also have exceptional resistance to both sulfuric acid and hydrochloric acid.
Because Hastelloy weld neck flanges resist some of the most severe media, Hastelloy weld neck flanges are often utilized in chemical processing applications where acid chlorides, solvents, formic and acetic acids, acetic anhydride, wet chlorine gas, hypochlorites, chlorine solutions and phosphoric acid are used. For chemical processing applications, Hastelloy C276 is the most common grade and one of the most corrosion resistant nickel alloys - exceeding that of most other nickel alloy grades like Inconel or Monel. For more indepth material information download our Hastelloy C276 datasheet.
Resources: Hastelloy Torque Spec, Flange Dimensions, Flange Bolting Chart
Flange Types Available: Blind Flanges, Lap Joint Flanges, Slip On Flanges, Socket Weld Flanges, Threaded Flanges, Weld Neck Flanges
Common Hastelloy Weld Neck Flange Grades
Confused about which grade of Hastelloy weld neck flanges are best for your corrosive application? Read this short blog post which gives an overview of each grade's strength. If you need more indepth direction, visit our Hastelloy grade pages or contact our engineering team.
Hastelloy C276 alloy, UNS N10276, is the most widely used and versatile, corrosion resistant alloy. Very good resistance to reducing, and mildly oxidizing corrosives. Excellent stress corrosion cracking resistance with very good resistance to localized attack. For more details about Hastelloy C276 download our datasheet..
Hastelloy C276 Specifications: N10276, ASTM B574, ASME SB574, Werkstoff 2.4819, ASTM G28-A/B, EN 10204-3.1, ASME B18.2.2, ASTM B619, ASME SB619, ASTM B366, ASME SB366, WPHC276, ASME B16.11, ASTM B564/ASME SB564, COLD DRAWN, HOT FINISHED, ASTM B575, ASME SB575, COLD ROLLED, HOT ROLLED, ASME B16.9, ASME B16.5, ASTM B462, ASME SB462
Hastelloy B3 alloy, UNS N10665, resistance to hydrochloric acid and other strongly reducing chemicals but has poor corrosion resistance to oxidizing chemicals and in the presence of ferric or cupric salts. In addition, Hastelloy B2 has excellent resistance to pitting and stress corrosion cracking. However B2 has little chromium, and it should NOT be used with oxidizing media in the presence of salts. Select the following links for more details about Hastelloy B2 Bolts, Screws, and Flanges.
Hastelloy B2 Specifications: N10665, ASTM B619, Werkstoff 2.4617, ASME SB619, ANNEALED, B/SB619 CLASS I OR II, X-RAY PER ASME SECTION VIII DIVISION 1 UW-51, MERCURY FREE, EN 10204-3.1, ASTM B366, ASME SB366, WPHB2-S, ASME B16.11, ASTM B335, ASME SB335, ASME B16.3, MSS SP-83, ASTM B564/ASME SB564, COLD DRAWN, HOT FINISHED, ASTM B333, ASME SB333, SHEET IS COLD ROLLED, HOT ROLLED, ENIMO-7, AWS A-5.11, ASME SFA-5.11
Hastelloy B3 alloy, UNS N10675, is specifically designed to deal with very aggressive hydrochloric acid (HCl), hyrdrobromic acid (HBr) and sulfuric acids (H2SO4) as well as acetic, formic and phosphoric acids. Additionally Hastelloy B3 has improved structural integrity over B2. However B3 has little chromium, and it should NOT be used with oxidizing media in the presence of salts. Select the following links for more details about Hastelloy B3 Bolts, Screws, and Flanges.
Hastelloy B3 Specifications: N10675, ASTM B366, ASME SB366, Werkstoff 2.4600, WPHB3-W, ASME B16.9, ANNEALED, MERCURY FREE, EN 10204-3.1 (W/O X-RAY), ASTM B335, ASME SB335, ASTM B564, ASME SB564, DIMENSIONS PER ASME B16.5, ASTM B462, ASME SB462, ASME B16.5, COLD DRAWN, HOT FINISHED, ASTM B626, ASME SB626, B/SB626 CLASS III, ASTM B333, ASME SB333, COLD ROLLED, HOT ROLLED
Hastelloy C22 alloy, UNS N06022, has better overall corrosion resistance in oxidizing corrosives than C-276 and Inconel 625 alloys due to the higher chromium content. Outstanding resistance to localized corrosion and excellent resistance to stress corrosion cracking. This alloy has limited availability and can be made into fastener in larger diameters only (1/2" and greater in size). Select the following links for more details about Hastelloy C22 Bolts, Screws, and Flanges.
Hastelloy C22 Specifications: SB 575/B 575, SB 574/B 574, SB 366/B 366 SB 462/B 462, SB 564/B 564 SB 462/B 462, Werkstoff 2.4602, 17744 No. 2.4602 NiCr21Mo14W, NACE MR0175 ISO 15156
Hastelloy C2000 alloy, UNS N06200, is a corrosion resistant alloy with excellent resistance to uniform corrosion in oxidizing or re-ducing environments. Due to the addition of copper and the high content of chromium, it has enhanced corrosion resistance to sulfuric acid and process streams contaminated with ferric ions. In addition it has excellent resistance to stress corrosion cracking and superior resistance to localized corrosion as compared to C-276 alloy.
Hastelloy C2000 Specifications: SB 575/B 575, SB 574/B 574, SB 366/B 366 SB 462/B 462,SB 564/B 564 SB 462/B 462, Werkstoff 2.4675, NACE MR0175 ISO 15156
Alloy X, UNS N06002, is most known for its exceptional combination of high temperature oxidation resistance up to 2000°C and high temperature strength. Being stable, strong and ductile at high temperatures are its most notable characteristics which is often utilized in gas turbine components and furnace components.
Hastelloy X Specifications: AMS 5536, AMS 5754, AMS 5798, ASME SB 435, ASME SB 572, ASME Sect. IX P No. 43, ASME Section IX P No. 43, ASME SFA 5.14, ASTM B 435, ASTM B 572, EN 2.4665, GE B50A436, GE B50T83, GE B50TF24, PDS 1038 (X-low), PDS 15102QFC, UNS N06002, Werkstoff 2.4665
MECHANICAL PROPERTIES OF HASTELLOY
Note:
(1) Use solution annealed material only.
(2) Not to be used over 1250 F.
(3) Use annealed material only.
(4) Not to be used over 1200 F. Alloy N06625 in the annealed condition is subject to servere loss of Imapact strength at room temperatures after exposure in the range of 1000 F to 1400 F.
(5) Grade 1.
(6) Not to be used over 800 F.
(7) Not to be used over 1000 F.
|
|
![]() |
![]() |
![]() |
Hastelloy Corrosion Data
Hastelloy C276 Iso-Corrosion Curves for HCl & H2SO4
Hastelloy Weld Neck Flange Features & Benefits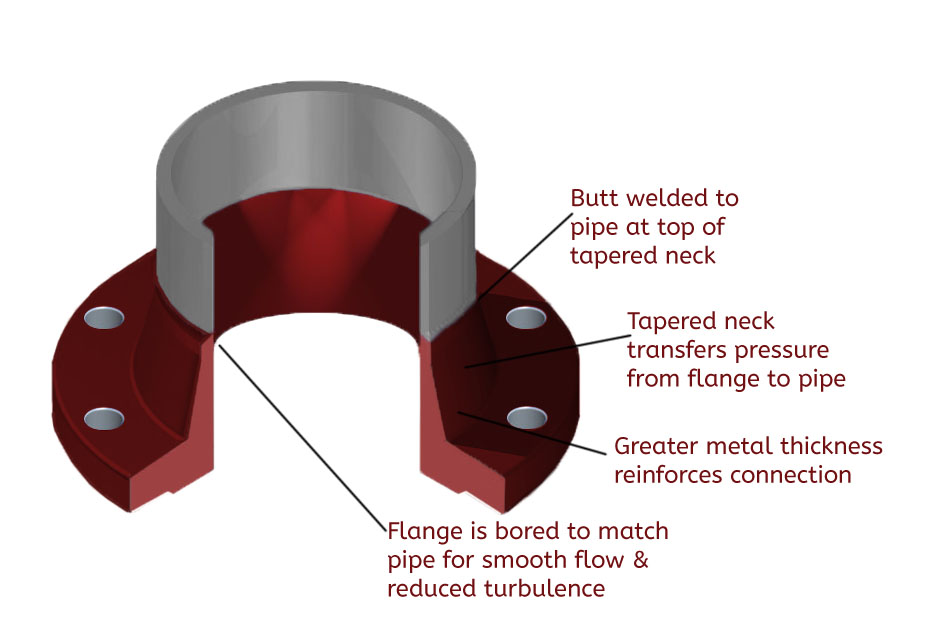
Hastelloy weld neck flanges are best for hazardous, high pressure applications. Weld neck flanges are easily identified by their long tapered neck. The inside of the flange is bored to match the inside diameter of the pipe in order to ensure there is no restriction in flow and also to prevent turbulence at the joint. The tapered neck provides thicker metal at the flange joint, while the neck narrows down gradually to meet the pipe where it is butt welded to the pipe. This design helps to transfer stress from the flange to the pipe, as well as diminish stress concentration at the base of the flange connection.
Hastelloy weld neck flanges are ideal for critical applications involving high pressure, sub-zero and elevated temperatures, as well as in conditions where fluctuations cause pipe expansion/contraction.
Key Feature: Ideal for high presure applications.
Weld Neck Flange Advantages
- Ability to withstand high pressure – since pipe is welded to the neck of the flange, stress is transferred to the pipe.
- The beveled end that, when connected to a pipe, creates a trough for a strong weld.
- Most versatile flange in the ASME stable of flanges.
Weld Neck Flange Disadvantages
- More advanced welding skill is needed for installation. The inside weld must be smooth to reduce friction and the outside weld must meet code criteria.
Uses
- Severe conditions that include high-pressure, high-cyclic and hazardous fluid applications.
- Fitting-to-fitting fabrication where the flange is welded directly to a fitting, such as an elbow, without the need for a short piece of pipe, as would be required with a slip-on flange.