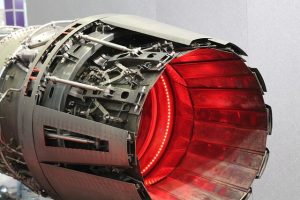
![]() |
Inconel 600 Bolts
High Temperature Resistance
• Ideal for oxidation and carburization resistance at high temperatures
• Good resistance to chlorine media such as dry chlorine, chloride-ion stress corrosion cracking and hydrogen chloride gases at moderate temperatures.
• Excellent for furnace components and chemical processing equipment.
Inconel 601
Excellent Mechanical Properties
• Similar oxidation and carburization resistance to grade 600 with improved high strength and mechanical toughness.
• 107 ksi tensile strength compared to 93ksi of grade 600.
• Good creep and rupture strength, as well as metallurgical stability in heat.
• Ability to stave off strain at high temperatures.
Inconel 625
Corrosion Resistance
• Best known for its high temperature corrosion resistance.
• Often used in chemical processing, nuclear power plants and oil & gas.
• Good resistance to harsh chemicals: sulfuric, hydrofluoric and phosphoric acids.
• Corrosion resistance is often comparable to that of Hastelloy C276.
Inconel 718
Superior Strength & Corrosion Resistance
• FAR exceeds all Inconel alloys and most materials available to industry in terms of high strength with the exception of a few alloys like MP35N.
• Extreme high strength with a min of 185ksi UTS and 150ksi yield strength per ASTM B637. A work hardened version that has min of 220 ksi UTS.
• Ideal for high strength, corrosive applications such as gas turbine engines, down-hole oil & gas and aerospace.