A Fe-Ni-Cr alloy with excellent high temperature oxidation resistance
- Good material for high temperature oxidation resistance
- Maintains high strength at elevated temperatures
- A286 Chemistry, specs, and heat treatments
- Weld neck flange features and benefits
A-286 weld neck flanges are known for their high strength, creep resistance and oxidation resistance at elevated temperatures. This iron-nickel-chromium alloy (once age-hardened) provides A-286 weld neck flanges with high levels of strength from room temperature up to about 1300°F (700°C).
A-286 weld neck flanges are mildly corrosion resistant. While they should not be used for strong acid environments, they provide excellent oxidation resistance up to 1300°F (700°C) in conditions that would typically be found in high temperature exhaust streams.
Because of these properties, A-286 weld neck flanges are often found in high temperature engine, manifold, exhaust and turbine applications as well as off-shore oil & gas applications.
Resources: A-286 Torque Specs, Flange Dimensions, Flange Bolting Chart
Flange Types Available: Blind Flanges, Lap Joint Flanges, Slip On Flanges, Socket Weld Flanges, Threaded Flanges, Weld Neck Flanges
A-286 Chemistry, Specifications & Heat Treatments
A-286 Heat Treatments: There are several heat treatment combinations for A-286 all with slight variations in performance. They can be specified via an AMS number or a 660 Class: A, B, C or D, with most common specified as class A or D. The A-286 grades A, B and C all have the same min tensile strength and min yield strength of 130ksi and 85ksi respectively. However grade D is significantly better yield with a min tensile of 130ksi and a min yield of 105ksi.
By AMS numbers, the most common for A-286 is AMS 5737 (same as Grade A) and then AMS 5732 (same as Grade B).
A-286 Specifications: AMS 5525, AMS 5732, AMS 5737, AMS 5804, EN 1.4980, GE B50T1181, GE B50T12, GE B50T81, UNS S66286, Werkstoff 1.4980
Mechanical Properties
A286 Weld Neck Flange Features & Benefits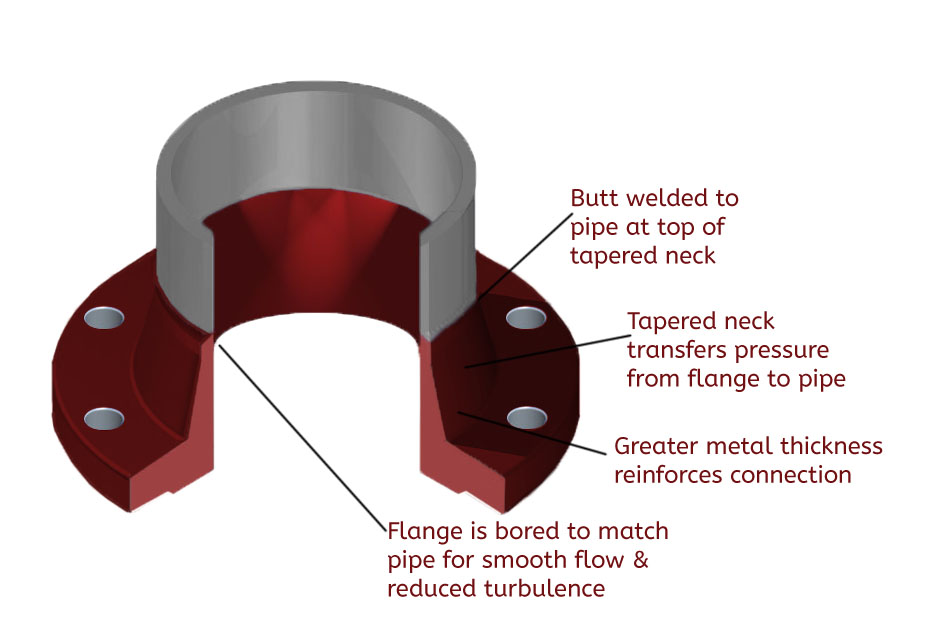
A286 weld neck flanges are best for hazardous, high pressure applications. Weld neck flanges are easily identified by their long tapered neck. The inside of the flange is bored to match the inside diameter of the pipe in order to ensure there is no restriction in flow and also to prevent turbulence at the joint. The tapered neck provides thicker metal at the flange joint, while the neck narrows down gradually to meet the pipe where it is butt welded to the pipe. This design helps to transfer stress from the flange to the pipe, as well as diminish stress concentration at the base of the flange connection.
A286 weld neck flanges are ideal for critical applications involving high pressure, sub-zero and elevated temperatures, as well as in conditions where fluctuations cause pipe expansion/contraction.
Key Feature: Ideal for high presure applications.
Weld Neck Flange Advantages
- Ability to withstand high pressure – since pipe is welded to the neck of the flange, stress is transferred to the pipe.
- The beveled end that, when connected to a pipe, creates a trough for a strong weld.
- Most versatile flange in the ASME stable of flanges.
Weld Neck Flange Disadvantages
- More advanced welding skill is needed for installation. The inside weld must be smooth to reduce friction and the outside weld must meet code criteria.
Uses
- Severe conditions that include high-pressure, high-cyclic and hazardous fluid applications.
- Fitting-to-fitting fabrication where the flange is welded directly to a fitting, such as an elbow, without the need for a short piece of pipe, as would be required with a slip-on flange.